Advantages and Impact Analysis of Liquid vs. Powder PCE on Concrete
by GIANT | Feb 13, 2025
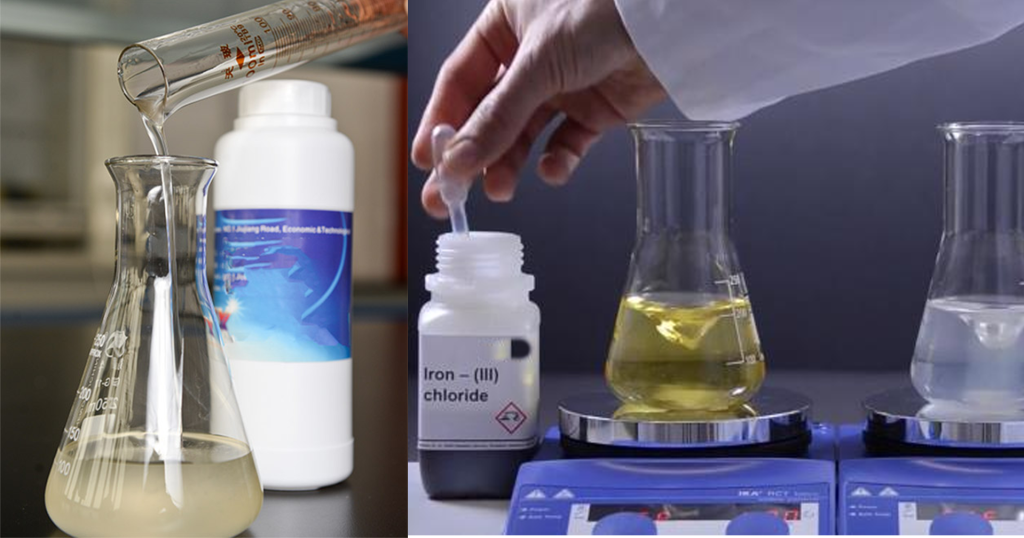
Polycarboxylate ether (PCE) superplasticizers, as a core material in modern concrete technology, exhibit distinct advantages and limitations in their liquid and powder forms. Below is a comparative analysis from production, performance, cost, and application scenarios to guide engineering decision-makers in selecting the appropriate form.
I. Advantages and Impact of Liquid PCE
- Production and Construction Convenience
- Direct Addition: No dissolution required; can be directly added via dosing pumps to mixers, suitable for automated mixing stations, reducing human error.
- Uniform Dispersion: Pre-dispersed molecular chains in water enable rapid bonding with cement particles, reducing concrete viscosity and improving workability.
- Case Study: Large commercial mixing stations widely adopt liquid PCE, with daily consumption at a single station exceeding 10 tons, compatible with automated systems.
- Performance
- Stable Water Reduction: Liquid PCE offers 2%–5% higher water reduction rates than equivalent powder formulations (especially at low dosages) due to stable molecular structures.
- Slump Retention: Less sensitive to high temperatures; 2-hour slump loss in summer can be controlled below 30mm.
- Limitations
- Storage and Transportation: Requires frost protection (crystallization risk below -5°C) and preservatives (biocides). Higher transportation costs due to 40%–50% water content.
- Short Shelf Life: Typically 6–12 months; performance may degrade in humid regions due to moisture absorption.
II. Advantages and Impact of Powder PCE
- Economic Storage and Transportation
- Compact Volume: Powder weight is 1/3 of liquid for equivalent active content, reducing transportation costs by over 50%.
- Long Shelf Life: 18–24 months in sealed, dry environments, ideal for remote areas or intermittent projects.
- Adaptability
- On-Site Mixing: Requires pre-dissolution (40°C warm water recommended) for small-scale projects or repair mortars.
- Customizable Formulations: Can be blended with retarders, air-entraining agents, etc., to meet specialized needs (e.g., ultra-retarded underwater concrete).
- Performance Considerations
- Dissolution Risks: Insufficient mixing may cause localized overdosing, leading to bleeding or retardation (ensure >3 minutes of dissolution time).
- Temperature Sensitivity: Slow dissolution in low temperatures may affect initial fluidity.
III. Key Performance Comparison
Parameter | Liquid PCE | Powder PCE |
---|---|---|
Water Reduction | 25%–35% (dosage 0.15%–0.3%) | 20%–30% (equivalent dosage) |
Slump Retention | <50mm loss in 1h (optimized for heat) | Requires additional slow-release components |
Compressive Strength | 15%–20% higher 3-day strength | Slightly lower early strength (delayed dissolution) |
Application | Large mixing stations, hot climates | Long-distance transport, multi-component blending |
IV. Selection Recommendations
- Prioritize Liquid PCE for:
- High-volume production (>1000 m³/day) with automation and stability requirements.
- High-temperature environments (e.g., Middle East, Southeast Asia) needing slump control.
- Prioritize Powder PCE for:
- Projects with >500 km transport distances or limited storage (e.g., remote African sites).
- Specialized engineering requiring functional additives (e.g., anti-clay agents, accelerators).
- Cost Comparison:
- Liquid: ~¥5,000–6,000/ton (incl. freight), suitable for short-haul, high-frequency use.
- Powder: ~¥8,000–10,000/ton, but higher active content per ton, more economical for long-haul transport.
V. Future Trends
- Liquid Dominance: Over 70% of new global mixing stations adopt automated liquid PCE systems.
- Functional Powders: High-purity powders (>98% purity) for specialty mortars and 3D-printed concrete.
Conclusion: Liquid PCE excels in large-scale projects, while powder PCE offers flexibility and storage advantages. Choose based on project scale, environmental conditions, and supply chain capabilities. Hybrid use (e.g., liquid at main stations, powder at satellite sites) may optimize outcomes.